lactose grinding design нь ball mill
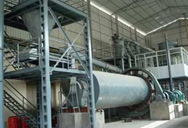
Original Research PaperBreakage, temperature dependency
2016.7.1 The solubility of Lactose increases (shown in Table 2) because of the rise of the temperatures in the planetary ball mill (not cooled during the grinding process) [18],
More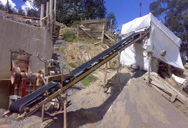
Breakage, temperature dependency and contamination of Lactose
2016.7.1 Additionally the recrystallization behaviour of Lactose was further investigated in a planetary ball mill and stirred media mill. With a sufficiently formulated
More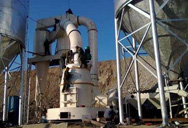
Energy-based analysis of milling α-lactose monohydrate
2004.4.1 Energy-based analysis of milling α-lactose monohydrate. Y.Chen1, Y.Ding1, D.G.Papadopoulos2, M.Ghadiri1. Show more. Add to Mendeley.
More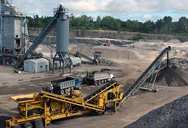
(PDF) Grinding in Ball Mills: Modeling and Process
2012.6.1 PDF The paper presents an overview of the current methodology and practice in modeling and control of the grinding
More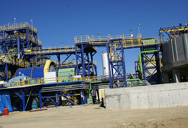
Grinding in Ball Mills: Modeling and Process Control
There are three types of grinding media that are commonly used in ball mills: • steel and other metal balls; • metal cylindrical bodies called cylpebs; • ceramic balls with regular or
More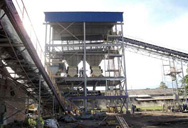
Intelligent optimal control system for ball mill grinding
2017.8.27 2 Grinding process description The ball mill grinding process is mainly composed of a ball mill, a hydrocyclone cluster, a sump, a slurry pump and an ore bin.
More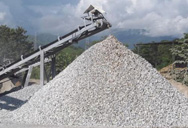
Modeling and Simulation of Whole Ball Mill Grinding Plant
2014.1.17 This paper introduces the development and implementation of a ball mill grinding circuit simulator, NEUSimMill. Compared to the existing simulators in this fiel
More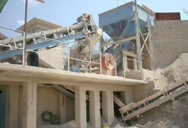
A CRITICAL REVIEW OF GRINDING DESIGN
2021.1.8 • Transfer size (T80) is the term used to describe the SAG mill product that is sent to the ball mill. For peak performance and balancing the power available in the
More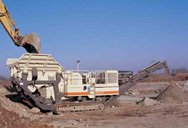
Investigating grinding mechanisms and scaling criteria in
2024.3.25 Three mechanisms are classically identified as responsible for the particle fragmentation in a ball mill: compression due to the weight of the pebbles bed, shearing
More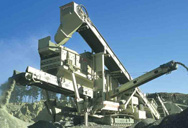
Rethinking Grinding Efficiency in Ball Mills - CEEC (Coalition
2024.4.8 Detailed DEM assessment comparing a conventional ball mill indicates that mil speed and shell liner design significantly impact the energy transfer for grinding,
More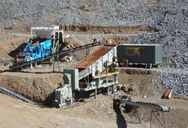
Lactose and dairy products - Hosokawa Alpine
Lactose and dairy products. Tailor-made solutions for the requirements of the dairy industry. From grinding to pulverising: The production of lactose and dairy products brings with it a number of challenges. Hygienic
More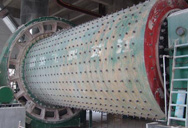
Grinding Mill Design Ball Mill Manufacturer
2017.2.20 Type CHRK is designed for primary autogenous grinding, where the large feed opening requires a hydrostatic trunnion shoe bearing. Small and batch grinding mills, with a diameter of 700 mm and more, are
More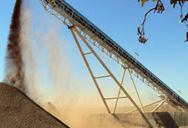
ball mill for lactose grinding design - fonz.co
The mill product can either be finished size ready for processing, or an intermediate size ready for final grinding in a rod mill, ball mill or pebble mill. AG/SAG mills can accomplish the same size reduction work as two or three stages of crushing and screening, a rod mill, and some or all of the work of a ball mill.
More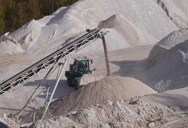
Dry Grinding Vs. Wet Ball Mill Grinding Economy Ball Mill
2023.9.15 Dry ball milling requires less energy than wet ball milling but has a lower throughput. Wet ball milling requires more energy than dry ball milling but also has higher throughput. . Dry ball milling is more efficient for materials that don’t require very fine particles or have a low tendency to group together.
More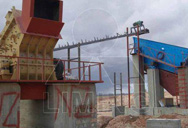
Ball Mill Design/Power Calculation - 911 Metallurgist
2015.6.19 The basic parameters used in ball mill design (power calculations), rod mill or any tumbling mill sizing are; material to be ground, characteristics, Bond Work Index, bulk density, specific density, desired mill tonnage capacity DTPH, operating % solids or pulp density, feed size as F80 and maximum ‘chunk size’, product size as P80 and maximum
More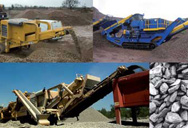
Industrial Ball Mill Grinders Pulva
Both continuous and batch style ball mills use centrifugal force, gravity and hard media to break up industrial materials into fine pieces or powder. Ball milling systems grind dry material and wet slurry alike. Each Pulva ball mill features a powerful motor that drives a gear system and causes the barrel to spin at 30-40 rotations per minute.
More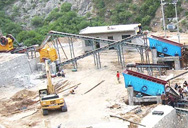
Horizontal Hammer Mill Grinding System Bühler Group
Complete grinding solutions for your needs. Bühler offers the full package for grinding lines for any situation. From sieving, conveying, storage, hoppers, gates, feeders, automation, fans, filters and safety equipment, we have you covered. We have industry-leading experience in design, installation and commissioning of grinding lines.
More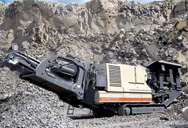
ball mill for lactose grinding design
2015.6.19 The basic parameters used in ball mill design (power calculations), rod mill or any tumbling mill ... A wet grinding ball mill in . Read More Grinding Mill Design Ball Mill Manufacturer. 2017.2.20 The grinding charge in a ball mill
More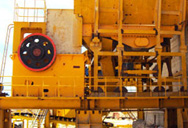
ball mill for lactose grinding design - labuticarne.es
Ball Mill For Lactose Grinding Design Ore Processing. Ball mill grinding theory ball mill for lactose grinding design mill grinding wikipedia a mill is a device that breaks solid materials into smaller pieces by grinding crushing or cutting rod mills are less common than ball mills for grinding minerals 44 134m diameter and a power of 35 mw 47000 hp has been
More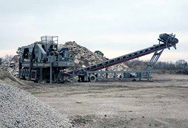
Design and Fabrication of Mini Ball Mill PDF Mill (Grinding ...
2023.3.2 Design and fabrication of Mini ball mill - Read online for free. Sjsj isis isis isis isis iaisi iajs has hsbs ahha haha fjck iakaj haj abab jH hana ja s f skak jaksnc akkajd ankaidcu anhejf jjsksvj maiwjr me know tnf akai vj w the tgnckzi the bana vusj and cj nks ajdbe a kr diya aur bs s levy at e with wah wah is.
More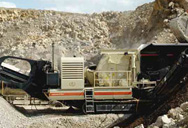
ball mill for lactose grinding design - viva-lite.es
and explains some of the key design criteria for making your own ball mill.Grinding Mill Design Ball Mill Manufacturer. Type CHRK is designed for primary autogenous grinding where the large feed opening requires a hydrostatic trunnion shoe bearing Small and batch grinding mills with a diameter of 700 mm and more are available These mills are of a
More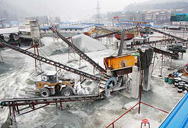
What is a Ball Mill? Economy Ball Mill
2023.6.12 What is a Ball Mill? A ball mill is a type of grinder that uses metal balls or other grinding mediums to reduce the size of various materials. The material to be ground is placed in a cylindrical container that spins on its axis. The metal balls or grinding media inside the container hits the material and breaks it down into smaller particles.
More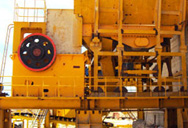
A CRITICAL REVIEW OF GRINDING DESIGN
2021.1.8 • Transfer size (T80) is the term used to describe the SAG mill product that is sent to the ball mill. For peak performance and balancing the power available in the SAG mill and ball mill, the transfer size must be measured and controlled. • The transfer size will be 500 microns using a 12mm opening trommel. This can be true under special
More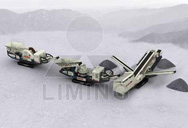
How grinding mill design changed over the last 30 years
2020.6.3 The design of such grinding mills is extremely critical, requiring sophisticated software tools, proprietary calculation worksheets, and experienced technical engineers and drafters. This blog will review how the mill design process has changed over the last 30 years. While most of the changes have been positive, new issues and problems have
More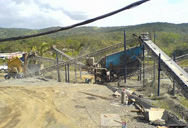
MODULE #5: FUNCTIONAL PERFOMANCE OF BALL
2018.12.9 • Ball mill specific grinding rate • Ball mill grinding efficiency The circuit output is defined as the production rate of fines by the circuit. It is calculated from three values: 1. The dry ore feed rate to the circuit (t/h). 2. The % fines in the circuit feed. 3. The % fines in the circuit product. Use this equation to solve for circuit ...
More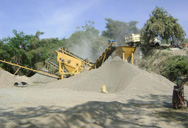
polysius® Ball Mill thyssenkrupp Polysius
The proven classical option for cement grinding. Whether employed as a two-compartment separator mill in an independent grinding system, or in combination with a high pressure grinding roll, the Ball Mill is a robust and reliable alternative for cement and granulated blast furnace slag grinding.. Used in combination with the sepol® high-efficiency separator,
More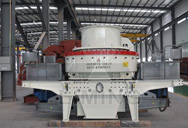
Principles of Grinding in Ball Mills - Orbis Machinery
The most desirable angle to accomplish this falls between 50 to 60° from horizontal. The lower end of this range applies to wet grinding applications for soft materials. The higher break point is reserved for harder wet grinding materials such as enamel as well as dry materials. This angle of break is also determinate upon the size of the mill.
More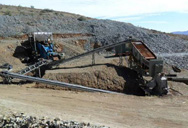
(PDF) Grinding in Ball Mills: Modeling and Process Control
2012.6.1 Grinding in ball mills is an important technological process applied to reduce the. size of particles which may have different nature and a wide diversity of physical, mechanical and chemical ...
More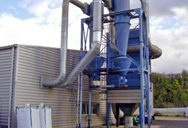
ball mill for grinding lactose - largoat
Grinding MachinesBall Mill Facebook. Grinding MachinesBall Mill. 645 likes 3 talking about this. Best turkey solution for mineral processing plant, best mineral processing machines...
More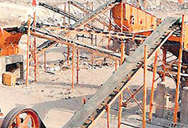
Grinding Ball Design - 911 Metallurgist
2017.11.6 Grinding Ball Design. Table of Contents. Grinding balls are essential mechanical components in ball and semiautogenous (SAG) mills. Their function is crushing and grinding ore rocks weighing up to 45 kg (100 lb) preparatory to recovery of valuable minerals, from lead through rare earth elements, which are essential to the approaching
More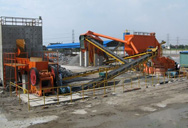
Grinding and granulation in a vibratory ball mill - ScienceDirect
1981.1.1 Abstract. In the grinding of paracetamol, lactose and sucrose in a vibratory ball mill, it is found that an equilibrium is rapidly attained due to the agglomeration of ground particles. The existence of this agglomerative phase of comminution has been extensively reported in the literature. This study investigates prolonged vibratory ball ...
More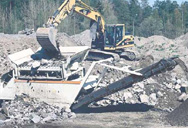
Analyzing the influence of lifter design and ball mill speed on ...
2023.10.30 Ball mills are the foremost equipment used for grinding in the mineral processing sector. Lifters are placed on the internal walls of the mill and are designed to lift the grinding media (balls ...
More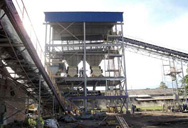
Ball Mill Is Indispensable For Lithium Ore Processing
4 天之前 The advantage of the grid type ball mill is that the ore discharge speed is fast, it can reduce the over-crushing of ore, and at the same time it can increase the output per unit volume. 1. Large row of ore mouth
More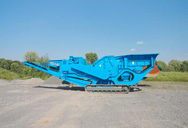
Ball Mill Liners Selection and Design Ball Mill Rubber Liner
2020.5.19 The ball mill liners are located on the inner surface of the ball mill barrel, which protects the barrel from the direct impact and friction of the grinding media and the material. The ball mill liners’ material and shape are different base on requirements. When the grinding media contacts different shapes of ball mill liners, the movement state will
More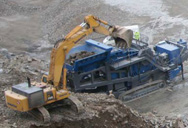
Grinding mills SKF
4 天之前 SKF offers solutions for autogenous mills, ball mills, high pressure grinding rolls, rod mills, SAG mils and horizontal grinding mills. The solutions are designed to protect pinions and trunnions and prevent failure in these harsh operating conditions – helping you improve reliability and safety while reducing maintenance and operating costs.
More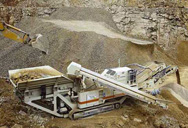
LACTOSE GRINDING - Bauermeister Size Reduction Equipment
Lactose Grinding. Milk is an emulsion of water, fat, protein and carbohydrates. The dissolved carbohydrates in milk are lactose molecules, a disaccharide often referred to as milk sugar. Milk contains up to 8 % lactose, which has a low sweetening power of around 25 % compared to sucrose. Industrially, lactose is won either in a direct ...
More
Factors Affecting the Grinding Efficiency of Ball Mills - Grinder
1. Speed of rotation. The rotation speed is an important parameter that directly affects the grinding efficiency of the ball mill. When the rotation rate is too low, the impact on the material will be small, which will lead to substandard fineness, thus affecting the grinding efficiency; when the rotation rate is too high, the impact energy of ...
More
Grinding in Ball Mills: Modeling and Process Control
There are three types of grinding media that are commonly used in ball mills: • steel and other metal balls; • metal cylindrical bodies called cylpebs; • ceramic balls with regular or high density. Steel and other metal balls are the most frequently used grinding media with sizes of the balls ranging from 10 to 150 mm in diameter [30].
More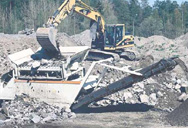
Breakage, temperature dependency and contamination of Lactose
2016.7.1 The solubility of Lactose increases (shown in Table 2) because of the rise of the temperatures in the planetary ball mill (not cooled during the grinding process) [18], [19]. Temperature measurements of the suspensions after 4 h milling in the planetary ball mill showed an increase of up to 10 °C (start temperature 19 °C).
More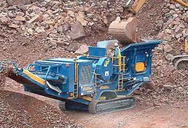
Sino Grinding Grinding Media Design, Manufacturing
Our SAG mill ball mill media are designed and optimized for our customers’ milling environments to improve steel consumption, wear rates, throughput and grind. ... throughput and grind. Tell me more about SGI’s products 7. SAG Mill Grinding Media Designs. 5. Ball Mill Grinding Media Designs. 20mm - 160 mm. Grinding Media Ø Size Range ...
More