vrm grinding Цемент
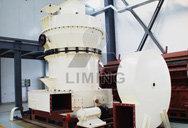
Review on vertical roller mill in cement industry its
2021.1.1 For the past three decades the vertical roller mill has emerged to be the preferred choice for grinding raw materials. With the grinding capacity of a vertical roller
More
Numerical Investigation of Vertical Roller Mill Operation
2023.12.4 Abstract. A vertical roller mill (VRM) is a grinding equipment used for the size reduction of minerals, cement, and ceramics. The capacity of the VRM depends not
More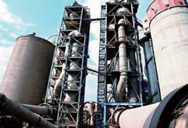
PROCESS CONTROL FOR CEMENT GRINDING IN
2017.10.27 The Vertical Roller Mill (VRM) reduces the power consumption for cement grinding approximately 30-40% associated with other grinding mills. The process
More
A cement Vertical Roller Mill modeling based on the
2022.10.1 Vertical roller mills (VRM) are widely used to grind, dry, and select powders from various materials in the cement, electric power, metallurgical, chemical, and
More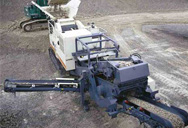
Review on vertical roller mill in cement industry its
2021.1.1 With the grinding capacity of a vertical roller mill and the ability to dry, grind and sort in a single unit, the vertical roller mill offers a definite advantage over the ball
More
Vertical Roller Mill Operation in Cement Plant
The vertical roller mill (VRM) is a type of grinding machine for raw material processing and cement grinding in the cement manufacturing process. In recent years, the VRM cement
More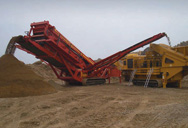
SikaGrind® for vertical roller mills
5 天之前 The production of Portland Cement (OPC, CEM I) with Vertical Roller Mills can demand the following benefits from a Grinding Aid: ́ Increased production rate, energy
More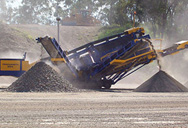
(PDF) Analysis and Optimization of Grinding Performance of
2022.1.23 PDF This work concentrates on the energy consumption and grinding energy efficiency of a laboratory vertical roller mill (VRM) under various operating...
More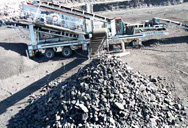
Improvement of cement performances through the use
2023.7.25 There is the possibility of further improvement of cement grinding in VRM. As described elsewhere [2], the use of grinding aids specifically formulated for the use in
More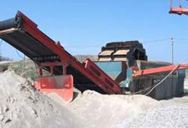
ENERGY EFFICIENT VRM TECHNOLOGY FOR CEMENT
2020.7.17 With the recent attention on environmentally friendly technology focused on CO2 emission reduction and energy efficiency, the demand for Vertical Roller Mills
More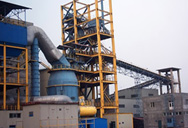
(PDF) LEARNING FROM OTHER INDUSTRIES; WHY THE VRM
2019.4.16 The vertical roller mill (VRM) is a comminution device in which crushing, grinding and classification processes are combine together into a single unit operation.
More
PROCESS CONTROL FOR CEMENT GRINDING IN VERTICAL ROLLER MILL ( VRM
The power ingesting of a grinding process is 50-60% in the cement production power consumption. The Vertical Roller Mill (VRM) reduces the power consumption for cement grinding approximately 30-40% associated with other grinding mills. The process variables in cement grinding process using VRM are strongly nonlinear and having large time delay
More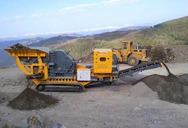
Operational parameters affecting the vertical roller mill
2017.4.1 Abstract. Vertical roller mills (VRM) have found applications mostly in cement grinding operations where they were used in raw meal and finish grinding stages and in power plants for coal grinding. The mill combines crushing, grinding, classification and if necessary drying operations in one unit and enables to decrease number of equipment
More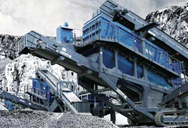
OK™ Raw and Cement Mill - FLSmidth
Our vertical roller mill offers optimum raw, cement and slag grinding. Our best-in-class OK™ Mill is a globally successful vertical roller mill solution for grinding raw material, cement and slag. Its cutting-edge design features consistently deliver the highest quality products with the greatest efficiency. It is affordable to install and ...
More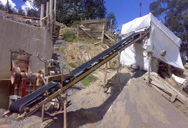
quadropol® thyssenkrupp Polysius Grinding Technologies
polysius ® grinding plants – a holistic approach. The development and, in particular, the enhancement of the quadropol ® concept incorporates the requirements of the market and is subject to a continuous development process. Cemento Progreso, Guatemala, 4500 tons per day plant incl. 2 x QMC² 51/25.
More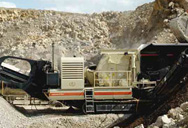
VRPM – AMCL Machinery Limited
The Vertical Roller Pre-grinding Mills developed by AMCL Machinery Limited are based on technical knowhow from Nihon Cement Co. Ltd. Japan. These machines are used for substantial power saving and capacity enhancement in the field of Clinker and Raw meal Grinding. We have over two decades of experience in supply and installations of Vertical ...
More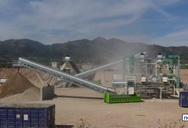
Predicting the grinding energy of vrm depending on material ...
2021.9.1 The grinding tests were performed with the pilot scale vertical roller mill located in the Loesche Test Center. The LM 3,6 type mill has 2 rollers and a nominal capacity of 707 kg/h. Set data and measured data during the grinding tests are controlled on-line by the automation system.
More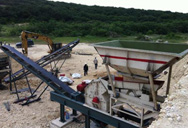
PROCESS CONTROL FOR CEMENT GRINDING IN
2017.10.27 The power ingesting of a grinding process is 50-60% in the cement production power consumption. The Vertical Roller Mill (VRM) reduces the power consumption for cement grinding approximately 30-40% associated with other grinding mills. The process variables in cement grinding process using VRM are strongly nonlinear and
More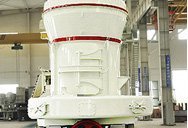
Cement grinding Vertical roller mills VS ball mills
However, the unit cost for wear parts for a ball mill is much lower than for a vertical roller mill. For a ball mill grinding OPC to a fineness of 3200 to 3600 cm2/g (Blaine) the cost of wear parts (ball, liners and mill internals) is typically 0.15-0.20 EUR per ton of cement.
More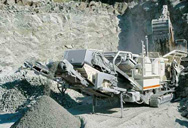
Energy-Efficient Technologies in Cement Grinding IntechOpen
2016.10.5 The energy consumption of the total grinding plant can be reduced by 20–30 % for cement clinker and 30–40 % for other raw materials. The overall grinding circuit efficiency and stability are improved. The maintenance cost of the ball mill is reduced as the lifetime of grinding media and partition grates is extended. 2.5.
More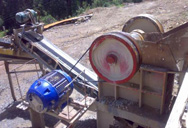
VRM audits and optimisation - International Cement Review
2021.11.16 VRM audits and optimisation. The increasing use of vertical roller mills (VRMs) in the production of cement to reduce power consumption and CO 2 emissions has resulted in an increasing need for VRM optimisation. As cement producers look to protect profits as well as their environmental reputation, a process audit can identify the root
More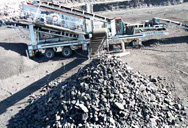
Review on vertical roller mill in cement industry its
2021.1.1 The feed size is generally 40 to 100 mm and can reach 120 mm in case of large VRM. In turn it simplifies the grinding system [15], [16]. • The effect of the thickness of the material layer between the rollers and the grinding table (called grinding bed). The thickness of the grinding bed will be as small as 1–2% of the roller diameter [15 ...
More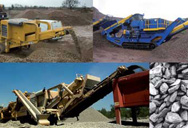
Comparing ball mills and VRMS for cement grinding
2013.2.26 The equipment costs are higher for a VRM than a ball mill, reflecting the greater complexity of the system, which includes items such as the rollers, table and the hydraulic system. Overall, when equipment,
More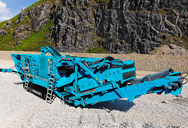
The VRM grinding circuit at Ilam cement plant - ResearchGate
The VRM has four rollers including two big rollers (master rollers) and two small rollers (slave roller), which respectively perform grinding and make material layering on the grinding table. Fig ...
More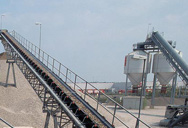
VERTICAL ROLLER MILLS A holistic VRM approach
2022.4.4 VRM for raw material grinding and two identical QMC² VRMs for cement grinding. Performance tests were executed over three days, and showed a smooth and reliable performance of both cement grinding systems. Cementos Progreso commented: “We are very satisfied with high reliability of the two cement mills, which ensures the
More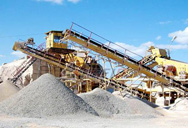
Cement grinding: VRM or ball mill? - LinkedIn
2019.2.9 Investment cost. A VRM is a compact unit, making the footprint of the installation smaller and reducing the civil engineering costs when compared to a ball mill system. Savings are also made due ...
More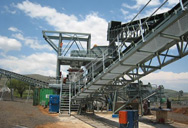
Progress with grinding aids for VRMs - Global Cement
2018.6.1 The optimum grinding aid is still, to a large extent, selected empirically. However, Sika has found that a deeper understanding of the mechanism of grinding aids from tests in a laboratory or pilot mills, 1 are helpful for selection. Testing at Loesche. Loesche GmbH is a leading VRM manufacturer for the cement sector.
More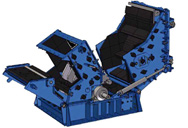
Coal mill, gypsum mill, clay mill, etc. Pfeiffer MPS mills
MPS 3070 BK coal mill, Jaypee Cement Balaji, India. MPS 180 GC vertical roller mill for the grinding, drying and calcining of gypsum, Knauf Knin, Croatia. MPS 100 GC vertical roller mill for the grinding, drying and calcining of gypsum, Trevo, Brasil. MPS 3350 B mill for limestone grinding, China Chongqing Foreign Trade Huaneng, China.
More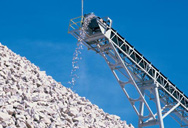
TRM SERIES SLAG VERTICAL ROLLER MILL TRM ...
2013.3.13 Slag VRM in China TRM series Slag VRM has the following characteristics in structure, operation and maintenance. Flat – inclined grinding table and cone type grinding roller Using static and dynamic high efficiency cage type separator To pressurize
More
Progress with Grinding Aids for Vertical Roller Mills - Sika
The differential pressure between the inlet and outlet of the mill (ΔP mill) is an important process variable for the testing of grinding aids.ΔP mill reflects the load and the filling level of the mill. At unchanged separator settings, the increase of ΔP mill indicates more internal circulations and more fines. As a result of the higher ΔP mill, the mill vibration increases
More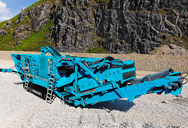
Modeling and simulation of vertical roller mill using
The VRM technology was introduced in the mid-'90s for grinding clinker and slag by LOESCHE (Schaefer, 2001). Fig. 1 illustrates the grinding parts of a Loesche vertical roller mill. The grinding material is comminuted in the Loesche roller grinding mill between the rotating horizontal grinding track and stationary grinding rollers.
More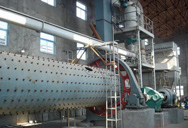
Review on vertical roller mill in cement industry its
2021.1.1 Comparison among grinding technologies - Ball mill V/s VRM. For the past three decades the vertical roller mill has emerged to be the preferred choice for grinding raw materials. With the grinding capacity of a vertical roller mill and the ability to dry, grind and sort in a single unit, the vertical roller mill offers a definite advantage over ...
More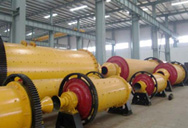
GET FIT FOR THE FUTURE - Loesche
2021.6.10 After inventing the vertical roller mill (VRM) in 1928, LOESCHE was the first to introduce the technology into the power, cement, steel, ore and minerals industry. Today more than 2,300 mills are in operation worldwide. The proven LOESCHE VRM provides lots of benefits for ore grinding. Adapted to the tough conditions in mining
More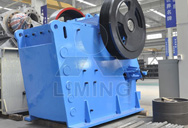
VRM optimisation - International Cement Review
2015.7.29 VRM optimisation. Most new cement plants utilise vertical roller mills (VRM) for raw material grinding and preparation. Taking a step-by-step look at the entire roller milling process, Kline Consulting recommends routine measurements and discusses ways to overcome chemical issues to optimise operations. • incorporation of drying with
More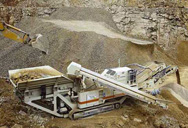
Application of Vertical Roller Mill in Cement Production
In the cement grinding process, VRMs are used to grind and crush the clinker and gypsum used to produce cement. Similar to the raw material grinding process, the clinkers are fed into the VRM and crushed by the rollers. The crushed clinker is then transported to a separator, where the fine powder is separated from the coarse particles.
More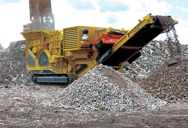
Roller Mill Based on Experimental Method - mdpi-res
2022.1.23 tion comparing conventional grinding systems and VRM in cement plants. It is worth noting that the VRM could save 30% energy in cement grinding [7–12]. In a test performed in the Loesche test center in Germany, copper slag grinding saved 22.9% energy in an air-swept model and 34.4% energy in an overflow model [13,14]. Altun also found this
More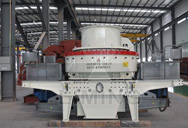
EVALUATION OF HPGR AND VRM FOR DRY
2024.3.28 VRM is in raw material for cement production and coal grinding, but there are very few examples of VRM usage within the broader mining industry: Schaefer [7] describes VRM grinding of phosphate, while Geroldet al. [8] report applications in copper matte, steel slag and tin slag grinding. There is a growing interest in both HPGR
More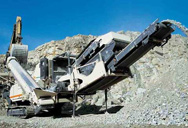
2 µm 5 µm - Loesche
2017.8.11 1985 Mills for grinding cement and granulated blast furnace slag were installed in Asia under licence from Loesche. 1994 The 2+2 technology, which was specially developed for grinding clinker and granulated blast furnace slag, was used for the first time in an LM 46.2+2 for cement grinding in the Pu Shin mill works of Lucky Cement, Taiwan.
More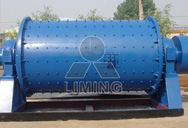
Mechanical behavior and modeling of grinding force: A
2023.9.29 The modeling of grinding force is helpful and imperative to decrease grinding heat, optimize grinding process, improve machining efficiency and product quality. 2.2. Grinding force model. Grinding force models are mathematical representations that depict the variation in force magnitude throughout the grinding.
More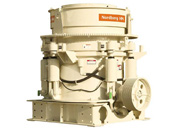
What is a vertical roller mill(VRM)? - Medium
2023.10.2 VRM grinding table metal casting part machining in progress. Grinding Rollers: Grinding roller is the main part for crushing and grinding materials.The grinding roller is composed of cast steel ...
More>> Next:мобильная дробильная станция 50 восьмисотых