диаграмма ball and race mill
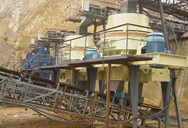
An analysis of ball-and-race milling. Part I. The hardgrove mill
1981.7.1 Figure 1 shows a ball-and-race mill [1] in which heavily loaded balls roll in a rotating race, subjecting powder in the race to high crushing forces. Feed enters the center of the rotating table and is thrown through the race by centrifugal action.
More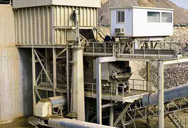
An analysis of ball-and-race milling part III. Scale-up to industrial mills
1982.9.1 SUMMARY The scale-up of breakage parameters measured in the Hardgrove mill to large mill diameters, using a simulation model for continuous milling, is
More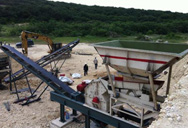
An analysis of ball-and-race milling part III. Scale-up to industrial mills
1982.9.1 The sub-models of comminution and classification for vertical spindle mill (VSM) presented in Part 1 of this paper have been integrated in the VSM simulation
More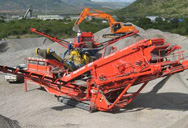
Ball And Race Mills - Rama University
2021.4.30 Ball And Race Mills In this mill the coal passes between the rotating elements again and again until it has been pulverized to desired degree of fineness. The
More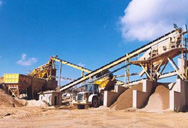
Coke and coal grinding in a ball race mill. Operational features
2001.5.3 Coke and coal grinding in a ball race mill. Operational features. Abstract: This paper gives a general description of the modern ball race mill, describes how shot
More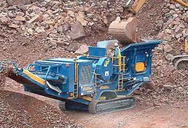
Adaptation of the Ball Race Mill Technology for Wet
2023.1.5 The influence of the quantity of fines present in the feed on grinding efficiency was also studied. A target cut point of 300μm was selected with the -300μm
More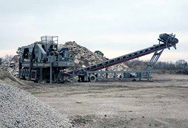
An analysis of ball-and-race milling. Part I. The hardgrove mill
Some Results on the Description of Size Reduction as a Rate Process in Various Mills. L. G. Austin K. Shoji V. K. Bhatia V. Jindal K. Savage R. Klimpel. Engineering, Chemistry.
More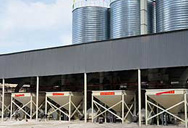
Effects of Ball Size Distribution and Mill Speed and Their Interactions ...
2020.7.2 An International Journal. Volume 42, 2021 - Issue 6. 833. Views. 1. CrossRef citations to date. 0. Altmetric. Research Article. Effects of Ball Size Distribution
More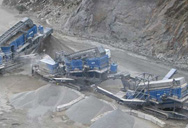
An analysis of ball-and-race milling part III. Scale-up to industrial mills
Coals used for power plants normally have different ash contents, and the breakage of coals by the ball-and-race mill or roller mill is an energy-intensive process. Grinding
More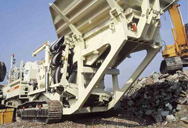
Investigation of the Breakage Properties of
1995.1.1 Investigation of the Breakage Properties of Components in Mixtures Ground in a Batch Ball-and-Race Mill. Heechan Cho; and ; Peter T. Luckie; Cite this: Energy Fuels 1995, 9, 1, 53–58. Publication Date
More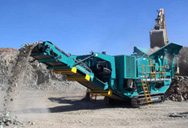
Ball And Race Mills - Rama University
2021.4.30 Ball And Race Mills In this mill the coal passes between the rotating elements again and again until it has been pulverized to desired degree of fineness. The coal is crushed between two moving surfaces, namely, balls and races. The upper stationary race and lower rotating race driven by a worm and gear hold the balls between them.
More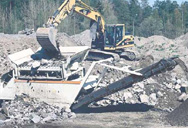
An analysis of ball-and-race milling part III. Scale-up to industrial mills
1982.9.1 Austin et al. in their series of papers [6–8], analysed a ball-and-race mill and derived a detailed model based on a scale-up of the Hardgrove mill to an industrial mill. Neal et al. [9] performed a frequency analysis of mill and boiler complex, and analyzed its effects on the steam pressure. Show abstract.
More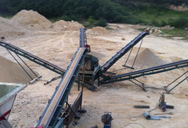
An analysis of ball-and-race milling part II. The babcock E 1.7 mill
1982.9.1 Abstract. A mathematical model was developed for a ball-and-race mill based on specific rates of breakage and primary fragment distributions. The model includes internal classification of particles falling back into the race and external classification due to the built-on classifier. It was demonstrated that the normalized primary fragment ...
More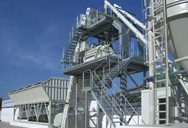
Critical Failure Analysis of Lower Grinding Ring of Ball
2018.9.14 The grinding ring was made of Ni Hard IV. Grinding ring of ball and race mill failed after giving the life only 2861 running hours. It was premature failure against the required useful life of 6500 running hours. The process of critical investigation of failure analysis includes visual observation, chemical analysis, microstructure analysis ...
More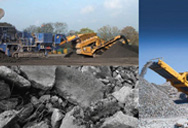
Investigation of Energy Consumed Characterization of
2016.10.22 Based on the energy balance calculation of heterogeneous grinding, energy split factors (ESFs) of components in the ball-and-race mill at different grinding time are firstly computed. These two energies are calculated by the modified model with parameters in the mixture and single breakage, respectively. Interaction between
More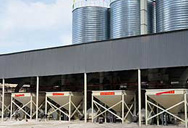
Ball Mills: An Overview - Raymer Engineering Corporation
2023.2.6 Ball mill is a kind of grinding machine that uses balls to grind and remove material. It contains a hollow compartment that rotates along a horizontal or vertical axis. It’s called a “ball mill” because it’s literally filled with balls. Materials are added to the ball mill, at which point the balls knock around inside the mill.
More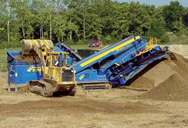
An analysis of ball-and-race milling part III. Scale-up to industrial mills
Coals used for power plants normally have different ash contents, and the breakage of coals by the ball-and-race mill or roller mill is an energy-intensive process. Grinding phenomena in mill of Expand. 5. PDF. Save. Simulation study of the energy-size reduction of MPS vertical spindle pulverizer.
More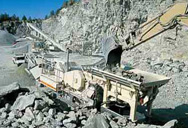
Reliable Coal Pulverizers and Mills » Babcock Wilcox
BW's coal pulverizers and mills set the standard for quality, durability, and superior performance, capable of accommodating a wide variety of coals and load swings. ... From our original E/EL ball-and-race type pulverizers for lower capacity applications, to the latest BW Roll Wheel™ pulverizer capable of grinding up to 230,000 pounds of ...
More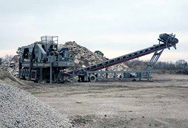
-Ball-and-race pulveriser (after Fern, 1982). - ResearchGate
-Ball-and-race pulveriser (after Fern, 1982). Source publication +1. 113 2010 Ozer Whiten Shi Dixen ... pulverising mill investigated in this study was an industrial scale ball-and-race pulveriser ...
More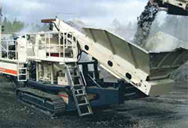
Ball And Race Mill [134wzw3rzm47] - Documents and E-books
Ball Race mill Namendra Anand Sr. Engineer (BM/RM) Ramagundam Super Thermal Power Station NTPC Limited nanan[email protected] Ramagundam Super Thermal Power Station NTPC Limited Milling system maintenance is a challenge as it requires to use all kinds of maintenance practices to run the system effectively. Its an opportunity as it
More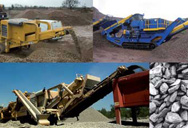
Industrial Ball Mill Grinders Pulva
Both continuous and batch style ball mills use centrifugal force, gravity and hard media to break up industrial materials into fine pieces or powder. Ball milling systems grind dry material and wet slurry alike. Each Pulva ball mill features a powerful motor that drives a gear system and causes the barrel to spin at 30-40 rotations per minute.
More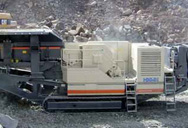
Ball Mill: Operating principles, components, Uses,
2022.11.30 A ball mill also known as pebble mill or tumbling mill is a milling machine that consists of a hallow cylinder containing balls; mounted on a metallic frame such that it can be rotated along its longitudinal axis.
More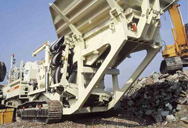
Investigation of the Breakage Properties of
1995.1.1 Investigation of the Breakage Properties of Components in Mixtures Ground in a Batch Ball-and-Race Mill. Heechan Cho; and ; Peter T. Luckie; Cite this: Energy Fuels 1995, 9, 1, 53–58. Publication Date
More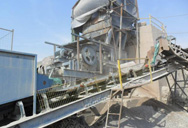
Adaptation of the Ball Race Mill Technology for Wet
2023.1.5 The influence of the quantity of fines present in the feed on grinding efficiency was also studied. A target cut point of 300μm was selected with the -300μm size fraction defined as “fines”. Table 5.7.1 below shows the controlled feed variable’s quantitative conditions and grinding rate, for 16 tests in total.
More
Construction and Working of Ball Mill - Solution Parmacy
2021.5.11 Construction of Ball Mill. The ball mill consists of a hollow metal cylinder mounted on a shaft and rotating about its horizontal axis. The cylinder can be made of metal, porcelain, or rubber. Inside the cylinder balls or pebbles are placed. The balls occupy between 30 and 50% of the volume of the cylinder. The diameter of the balls depends on ...
More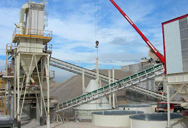
Changing the Fineness of Calcined Petroleum Coke with Ball Race Mills ...
2019.2.16 The test mill is a ball race mill type EM17-525. It has 5 balls of 250 mm diameter. This is the smallest industrial size of Claudius Peters EM-Mills. As bigger industrial CPC mills produce not more than 30 t/h up to now, the EM17 test mill allows precise predictions with a rather low scale-up factor of usually less than 100.
More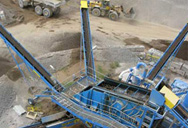
Ball and Race Mill PDF Industries Mechanical Engineering
2024.2.23 1. The document discusses maintenance practices for a ball and race mill used in a coal-fired power plant. 2. It describes preventative, predictive, proactive, and planned maintenance approaches used to maximize availability and minimize downtime. 3. Key aspects covered include preventative maintenance checks, vibration analysis, wear
More
Energy Engineering Questions and Answers – Pulverised Mills
2 天之前 Explanation: The pulverization or crushing action in ball and race mill takes between the two moving surfaces called balls and races. The rolling action happens between these two. Then the coal passes between the rotating elements time and again until it has been pulverized to the desired degree of fineness. 7. The pulverization is
More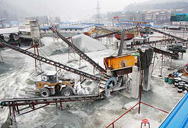
What is a Ball Mill? Economy Ball Mill
2023.6.12 What is a Ball Mill? A ball mill is a type of grinder that uses metal balls or other grinding mediums to reduce the size of various materials. The material to be ground is placed in a cylindrical container that spins on its axis. The metal balls or grinding media inside the container hits the material and breaks it down into smaller particles.
More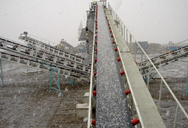
Ball Mill - an overview ScienceDirect Topics
where d b.max is the maximum size of feed (mm); σ is compression strength (MPa); E is modulus of elasticity (MPa); ρb is density of material of balls (kg/m 3); D is inner diameter of the mill body (m).. Generally, a maximum allowed ball size is situated in the range from D /18 to D/24.. The degree of filling the mill with balls also influences productivity of the mill
More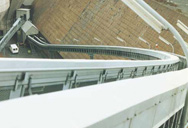
Pulveriser in Thermal Power Plant Bowl Mill Ball Mill
6 天之前 The Ball mill pulveriser is basically horizontal cylindrical tube rotating at low speed on its axis, whose length is slightly more to its diameter. The inside of the Cylinder shell is fitted with heavy cast liners and is filled with cast or forged balls for grinding, to approximately 1/3 of the diameter. Raw coal to be ground is fed from the ...
More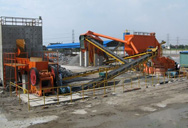
Ball Mill Grinding Machines: Working Principle, Types, Parts ...
A ball mill consists of various components that work together to facilitate grinding operations. The key parts include the following: Mill Shell: The cylindrical shell provides a protective and structural enclosure for the mill. It is often made of steel and lined with wear-resistant materials to prolong its lifespan.
More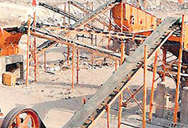
Analyses of the energy-size reduction of mixtures of
DOI: 10.1016/J.APT.2018.02.031 Corpus ID: 139635331; Analyses of the energy-size reduction of mixtures of narrowly sized coals in a ball-and-race mill @article{Sun2018AnalysesOT, title={Analyses of the energy-size reduction of mixtures of narrowly sized coals in a ball-and-race mill}, author={Xiaolu Sun and Weining Xie and
More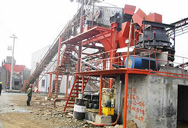
Ball Mill - Principle, Construction, Working, and More - Soln
2024.4.17 A pharmaceutical ball mill is a type of grinder used to grind and blend materials while manufacturing various dosage forms. The size reduction is done by impact as the balls drop from near the top of the shell. Ball mills are used primarily for single-stage fine grinding, regrinding, and as the second stage in two-stage grinding circuits.
More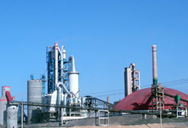
A multi-component model for the vertical spindle mill
2016.3.10 Effect of particle properties on the energy-size reduction of coal in the ball-and-race mill. 2018, Powder Technology. Citation Excerpt : Improvement of grinding efficiency and reducing energy consumption should base on a good understanding of energy-size reduction process. Though coal power plants make great contributions to
More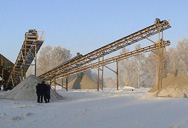
The Ultimate Guide to Understanding Ball Mill Diagrams
A ball mill diagram is a schematic representation of the cylindrical container that contains grinding media (balls) and the material to be ground. The diagram includes the rotating drum or cylinder, which is filled with grinding media and the material to be ground. The media and material are rotated to generate a tumbling action, causing the ...
More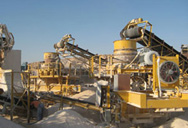
Analyses of the energy-size reduction of mixtures of
我们已与文献出版商建立了直接购买合作。 你可以通过身份认证进行实名认证,认证成功后本次下载的费用将由您所在的图书馆支付 您可以直接购买此文献,1~5即可下载全文,部分资源由于网络原因可能需要更长时间,请您耐心等待哦~
More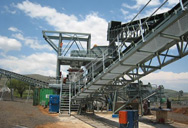
Dynamics of ball and rock charge in SAG mills - 百度学术
作者:. RK Rajamani , BK Mishra. 摘要:. The need to improve the technology associated with traditional methods of crushing and grinding has been an undisputed area of debate. Yet, there is very little structural and design improvement for increased capacity and energy utilization of the mill. This paper discusses the results of some of ...
More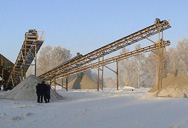
Modelling of vertical spindle mills. Part 2: Integrated models
2015.3.1 The main difference is that the ball-race design uses steel balls whilst the roller-race design uses rollers. This does not affect the structure of the models but the different pulveriser designs require slightly different calculations. As discussed in Part 1 of the paper, a VSM operation consists of three basic. E-mill (ball-race) model
More