coal pulveriser mills performance
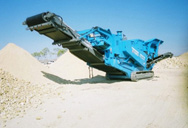
Pulveriser Mill Performance Analysis Optimisation in
2018.9.24 Pulveriser mill are one of the critical equipment of coal. fired thermal power plant. They are required to feed pulverized coal in required quality and quantity to meet
More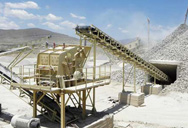
“Blueprint” Your Pulverizer for Improved Performance
2020.8.27 performance is governed by uniform coal combustion by the burn-ers and satisfactory coal fineness. Adequate fineness for both west-7. Optimum design. Ensure
More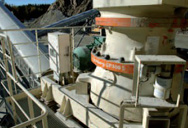
BW ROLL WHEEL PULVERIZERS - Babcock Wilcox
2021.10.5 Up to 230,000 lb/hr (104,300 kg/hr) Based on 50 HGI coal and 70% passing 200 mesh sieve (70% passing 74 micron) Design features for new and retrofit
More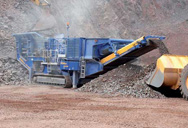
Optimisation of coal fineness in pulverised-fuel boilers
2017.11.15 Abstract. A method for choosing the optimum fineness of coal in pulverised-fuel boilers is presented. This method is based on economic criteria and takes
More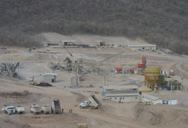
Industrial Coal Pulverizer Model Simulation and Parametric ...
2018.1.1 Abstract. The coal-pulverizer is an important unit, which pre-processes coal-fuel fed to the boiler in coal-based thermal power plants. It is extremely important to
More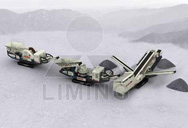
Improving Coal Pulverizer Performance and Reliability
2023.7.5 Description. Pulverization is currently the favored method of preparing coal for burning. Mechanically pulverizing coal into a fine powder enables it to be burned like
More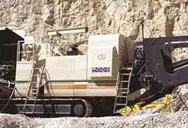
CFD based investigations into optimization of coal pulveriser ...
2009.9.1 Abstract. In coal-fired power plant, pulveriser is the first major component, whose performance dictates the total power plant efficiency. Uniform flow rate and
More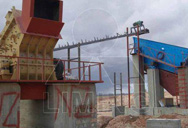
Boiler Mill and Coal Pulverizer Performance GE Steam Power
5 天之前 We’re a world leader in coal pulverizing and boiler mill operations for horizontal and vertical boiler mills—committed to high-efficiency performance, reduced
More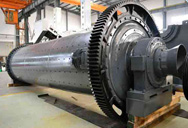
Performance optimisation of vertical spindle coal
2018.3.5 The effect of low calorific value coal was observed on mill’s response to match the boiler energy requirements. Evaluation of the current operating pulveriser data
More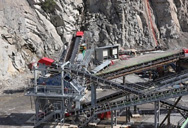
Reliable Coal Pulverizers and Mills » Babcock Wilcox
Reliable coal pulverizer performance is essential for sustained full-load operation of today's power plants. An effective pulverizer must be capable of handling a wide variety of coals
More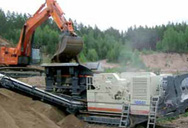
Performance optimisation of vertical spindle coal
2018.3.5 The mill outputs, pulverised coal fineness and distribution tests were carried out and evaluated from the data measured during plants tests. A mathematical spreadsheet was used to observe mill performance when operating parameters are varied. A mill’s heat balance evaluation was done using an Excel spreadsheet to evaluate the mill drying ...
More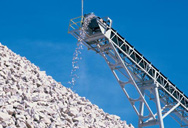
CFD Modeling of MPS Coal Mill for Improved
2009.1.1 CFD modeling of MPS coal mill with moisture evaporation. Coal pulverizers play an important role in the functioning and performance of a PC-fired boiler. The main functions of a pulverizer are ...
More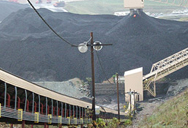
CFD based investigations into optimization of coal pulveriser ...
2009.9.1 In a coal-fired power plant, one of the main equipment is the coal mill, whose effectiveness influences mainly the whole power plant performance (Shah, Vuthaluru, and Vuthaluru 2009). These plants ...
More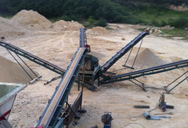
Mitsubishi Power Pulverizers
4 天之前 Supported fuels. Coal (Bituminous coal, subbituminous coal), biomass, PC (petroleum coke) Capacity. 9-145t/h. Fineness of pulverized coal. 70-95% pass through a 200 mesh screen. Classification methods. Rotating Separator / Fixed Separator / Combined Rotating + Fixed Separator. Information about Pulverizers from Mitsubishi Power.
More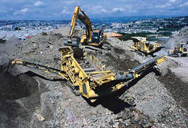
CFD based investigations into optimization of coal pulveriser ...
2009.9.1 Semantic Scholar extracted view of "CFD based investigations into optimization of coal pulveriser performance: Effect of classifier vane settings" by K. Shah et al. ... ABSTRACT This study shows the performance of a currently running vertical roller coal mill (VRM) in an existing coal-fired power plant. In a power plant, the coal mill is the ...
More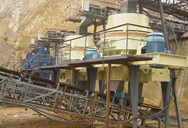
Pulveriser Mill Performance Analysis Optimisation in
2018.9.24 The milling system is an important. part of the auxiliary equipment of a coal-fired power plant. Pulveriser mill are one of the critical equipment of coal. fired thermal power plant. They are required to feed pulverized coal in required quality and quantity to meet boiler. steam output and eventually power generation.
More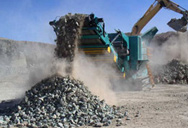
CFD based investigations into optimization of coal pulveriser ...
2009.9.1 In coal-fired power plant, pulveriser is the first major component, whose performance dictates the total power plant efficiency. Uniform flow rate and desired size fraction at outlet pipes along with higher classifier efficiency are three important measures which decide the pulverizer performance. Optimization of pulverizer at its best operating
More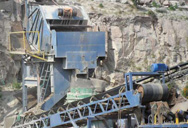
The Coal mill performance monitoring PPT - SlideShare
2019.11.27 0 likes • 2,513 views. Manohar Tatwawadi. Follow. The presentation covers the capacity of the coal mill wrt the grindebility index, the PA flow, coal flow, fuel air ratio etc. Engineering. 1 of 33. Download now. Download to read offline. The Coal mill performance monitoring - Download as a PDF or view online for free.
More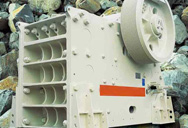
Multiphase flow simulation of a simplified coal pulveriser
2005.7.25 2001. TLDR. Flow Modeling for Reactor Engineering and Flow Modeling and Applications, a meta-modelling guide to reactor engineering and flow modeling, and applications for reactor design and engineering. Expand. 542. Semantic Scholar extracted view of "Multiphase flow simulation of a simplified coal pulveriser" by H. Vuthaluru et al.
More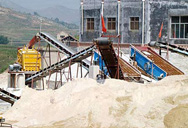
Optimisation of the performance of a new vertical roller mill
2024.1.15 Sun et al. [9] carried out study of a roller mill (HRM 4800 by Hefei Zhong Ya, China) and analysed air flow patterns in the mill to improve the energy efficiency of the mill. Shah et al. [ 10 ] used modelling to optimise the performance of a coal pulveriser by studying the influence of variation in inlet vane angles on the collection efficiency ...
More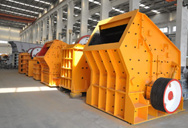
Modelling of vertical spindle mills. Part 2: Integrated models
2015.3.1 The BW E10 pulveriser is a common design and is the pulveriser used in the 350 MW power generation units at an Australian power station in Queensland. A schematic of this pulveriser design is shown in Fig. 1. The pulveriser is air-swept in which the coal is fed onto a rotating table through a central pipe.
More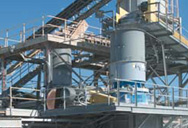
Improved Coal Fineness Improves Performance, Reduces Emissions
2011.10.1 Reducing the pulverized coal particle size (in particular, eliminating the coarse particles) increases the surface area to volume or mass ratio, effectively making the coal more reactive ...
More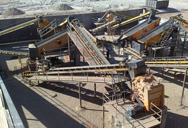
An investigation of performance characteristics
2020.8.12 Ultimately, the energetic efficiency of coal mill has been investigated and performance value has been found to be a maximum value of 96.2%. The layout of the coal mill with a rotary classifier ...
More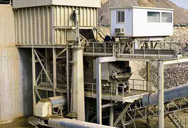
A Comparison of Three Types of Coal Pulverizers
2024.2.19 The BTM is a low-speed mill that primarily grinds coal by impact and attrition. The VRM is a medium- speed mill that grinds coal by compression and, because of the low coal inventory in the mill and flat grinding surfaces, develops shearing action as well. For both mills a constant centrifugal force is maintained. The speed
More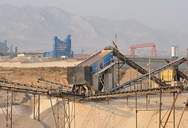
“Blueprint” Your Pulverizer for Improved Performance
2020.8.27 performance is governed by uniform coal combustion by the burn-ers and satisfactory coal fineness. Adequate fineness for both west-7. Optimum design. Ensure optimum arrangement of the mill throat and the coal flow path to improve mill performance. Source: Storm Technologies Inc. Grinding surface Finer particles and air to rise to
More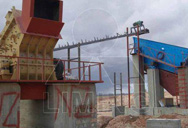
Optimisation of coal fineness in pulverised-fuel boilers
2017.11.15 In typical installations for coal n = 0.8–1.2, where the lower values correspond to high-speed pulverisers (e.g. fan mills), while the higher numbers correspond to the medium- and low-speed mills. For the pulverized fuel with the same content of particles >88 μm, e.g. R0.09 = 30%, the following contents of grains >200 μm are
More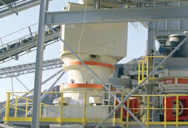
Predicting Pulveriser Performance
2017.10.3 The HGI is included in most thermal/PCI coal specifications as the indicator of mill performance. While HGI is adequate to characterise the grinding of most coals, some Australian coals can be disadvantaged as the HGI will indicate higher power requirements, lower throughputs and /or a coarser size distribution than actual.
More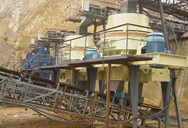
Multiphase flow simulation of a simplified coal pulveriser
2005.7.1 In coal-fired power plants, the first major component is pulveriser, whose performance dictates the total power station efficiency. Pulveriser is employed to grind the lumped coal and transport ...
More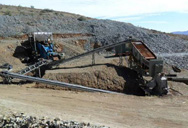
The Influence of Mill Loading on the Distribution of Pulverized Coal ...
2023.9.1 The results of the simulation show that increasing the capacity of the mill affects the increase of pulverized coal in the second exit of the separator by 5,75% and raising the flame. Greater granulation of pulverized coal has the consequence of increasing recirculation in the mill by 16,06%.
More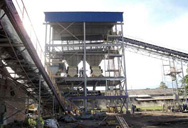
Coal mill pulverizer in thermal power plants PPT - SlideShare
2012.11.17 20. 13.1.Fineness Fineness is an indicator of the quality of the pulverizer action. Specifically, fineness is a measurement of the percentage of a coal sample that passes through a set of test sieves usually designated at 50, 100, and 200 mesh A 70% coal sample passing through a 200 mesh screen indicates optimum mill performance. The mill
More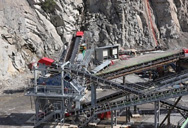
Investigation of wear pattern in a complex coal pulveriser using CFD ...
2006.8.1 1.. IntroductionThe power requirement, the throughput rate of a fossil fuel and the wear rate of the internal components of the mill directly affect the operating cost of a milling plant [1].Commercial considerations and the need to comply with the increasingly stringent environmental regulations are challenging the existing design and performance
More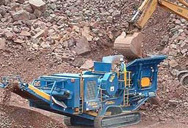
Model predictive control for an industrial coal pulveriser ...
2021.9.6 The coal-pulveriser/coal-mill is an important subsystem upstream of boilers in coal-based thermal power plants. The efficient boiler operations demand optimum combustion-air to coal-fuel ratio (AFR). In fact, portion of (preheated) combustion-air called primary-air, passes through coal-mill and carries pulverised coal to the boiler. The safe,
More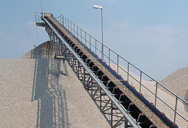
Improving Coal Pulverizer Performance and Reliability
2023.7.5 Coal is introduced through two hollow trunnions on each side of the tube. As the tube rotates, the balls tumble onto the coal,crushing and pulverizing it. Impact Mills Grinding Action is carried out by aseries of hinged or fixed hammers revolving in an Improving Coal Pulverizer Performance and Reliability Coal Conveyer Coal Crusher Raw
More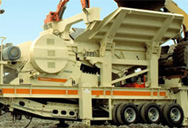
Investigation of wear pattern in a complex coal pulveriser
2006.8.1 The coal, which is pulverized in the mills, is transported and distributed by the primary gas through the mill-ducts to the interior of the furnace. This is done with a double function: dry and enter the coal by different levels for optimizing the combustion in the sense that a complete combustion occurs with homogeneous heat fluxes to the walls.
More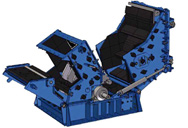
Optimisation of coal fineness in pulverised-fuel boilers
2017.11.15 output of operating mill [Mg/h] c f, unit coal cost [PLN/Mg] c m. unit cost of materials used for repairs/overhauls and operation of mills [PLN/kg] c mh. cost of man-hour [PLN/mh] d. ball diameter [mm] e pm. energy consumption of the pulveriser [kWh/Mg] e pw. energy consumption of the pulverized fan [kWh/Mg] I fg. enthalpy of flue gas leaving ...
More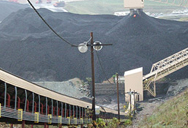
Investigation of wear pattern in a complex coal pulveriser using CFD ...
2006.8.1 The pulverization of coal into fine particles is made in ventilation mills (coal pulveriser) to increase the specific surface area to optimize the rate of heat and mass transfer between the coal ...
More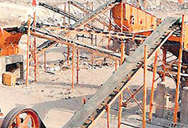
Technical specification for Procurement of Wear Parts
2023.7.11 3.0 Intending bidder must have experience of having successfully executed supply of vertical type coal pulveriser / grinding elements for coal mills during last seven (7) years prior to the date of techno- commercial bid opening with either of the following: a) One order costing not less than Rs. 579.46 lakhs.
More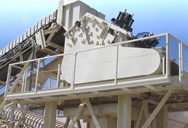
Coal Pulveriser Mills Performance - budspaw
Coal Pulveriser Mills Performance We provide crushing grinding products and solutions . CRM Mining Crusher is a Porland company with facilities in Europe and Africa that manufactures and installs crushing, grinding, and screening equipment and spare parts for mining, quarrying and demolition operations.
More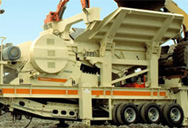
Home - GPL
We provide trusted service in fabrication, Manufacturing, Engineering and Assembly of Coal Pulverizing Mills used in Thermal Power Projects. Kappati is a market leader in the field of manufacture of Assemblies , OM replacement parts, Engineering, and servicing for Coal Pulverizers RP, RPS, HP Mills form 603 to 1203 size used in 60 MW to 800 MW Power
More